We engineer & manufacture
high-quality
wet (vapor) slurry blasting & high-pressure water systems.
LEADING VAPOR BLASTING TECHNOLOGY & INNOVATION SINCE 1999
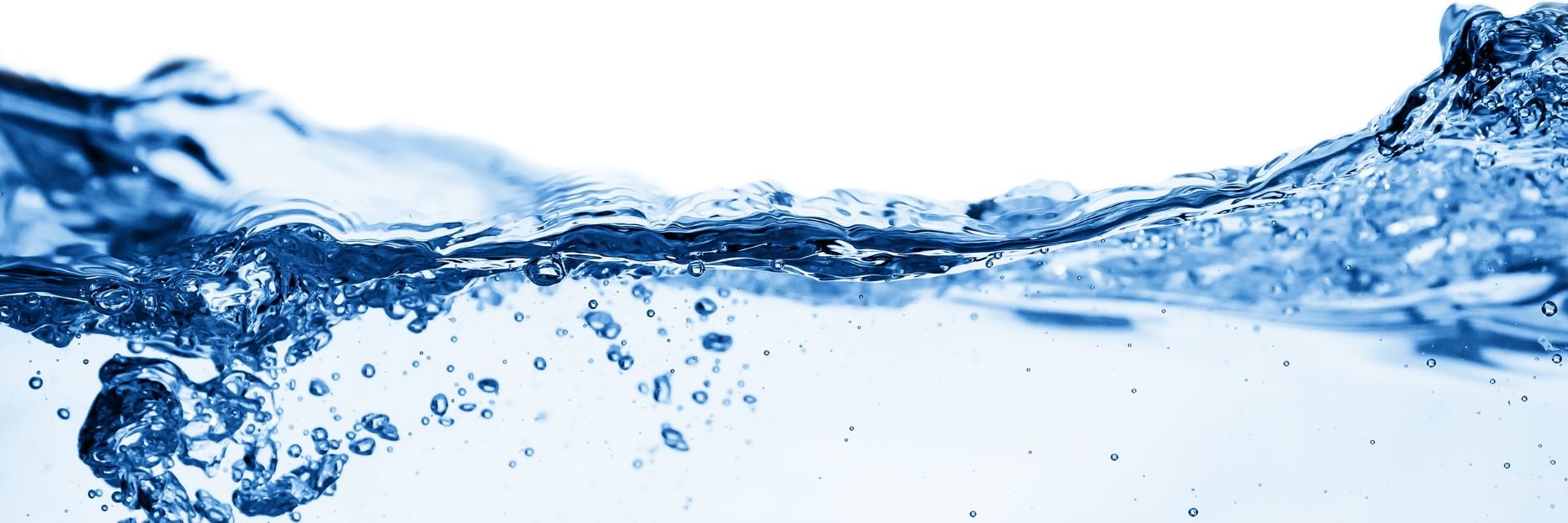
We can customize a solution for any application tailored to your finishing process needs.
BEFORE & AFTER USING A WET TECHNOLOGIES® SYSTEM
A vapor blasting system by Wet Technologies is dirt-free, sand-free, dust-free, & hassle-free.
Leaders in Slurry Blasting Technology
Our custom built cabinets have the ability to run the highest concentrations in the industry.
Our slurry delivery system provides the most even finishes with faster process times, and lower consumption rates.
Our compact footprints enable you to integrate this time and money saving right onto your production floor.
No more costly outsourcing, and no more in-house hazards from using dry abrasives.
Industrial applications include extensive cleaning, degreasing, deburring and descaling, as well as removal of paint, chemicals and oxidation, high-precision composite etching for bonding, and more.
The Company We Keep
Custom Industries & Applications
Aerospace & Aviation MRO
Automotive REMAN & Restoration
Coins &
Precious Metals
Firearms
Marine
Medical
Military MX & Defense
Why all vapor blasting systems are not created equal.
Each Wet Technologies® vapor blast system is engineered to meet your unique requirements and built with a high quality pump— the heartbeat of our blasting process.
Customer Testimonials
“It can take a part that’s 40-50 years old and make it look brand new. "
Haydon Brother’s Automotive, Anaheim, CA
Manual WT50SS Cabinet
Installed 2015 still in use today.
ENHANCE WORKER SAFETY
ELIMINATE DUST COLLECTORS & RISK OF IGNITION
ELIMINATE EXHAUST SYSTEM & DUCTS
SAVE FACTORY FLOOR SPACE
CREATE A MORE EFFICIENT WORKFLOW
REDUCE PROCESS STEPS
ELIMINATE EMBEDDED MEDIA & CONTAMINANTS
REDUCE MEDIA CONSUMPTION EXPENSES
ENHANCE WORKER SAFETY ELIMINATE DUST COLLECTORS & RISK OF IGNITION ELIMINATE EXHAUST SYSTEM & DUCTS SAVE FACTORY FLOOR SPACE CREATE A MORE EFFICIENT WORKFLOW REDUCE PROCESS STEPS ELIMINATE EMBEDDED MEDIA & CONTAMINANTS REDUCE MEDIA CONSUMPTION EXPENSES
Low maintenance vapor blasting cabinets to stand the test of time.
Not sure where to start?
A dedicated member of our team will walk you through the process every step of the way.
From selecting your cabinet’s personalized options, through building and testing your system, our team is here to ensure a trusted and precise finished product is made to your satisfaction.
Our products are high quality and low maintenance, meaning they are built to last for years.
We have been in business since 1999, with a majority of our systems still running today. We provide dedicated hands on training, and warrantied tech service support throughout the life of your cabinet.